As the building industry is ramping up its efforts to minimize embodied carbon emissions, structural elements have been the main focus. Embodied emissions from insulation materials have gained less attention. On January 1st, 2021, Environment and Climate Change Canada prohibited using hydrofluorocarbon (HFC) blowing agents in foam insulation products, notably spray foam insulation and rigid board insulation such as the popular XPS. This was an important step toward reducing embodied carbon of certain insulation materials. Project teams can reduce these emissions even further by better understanding low-carbon and carbon-storing insulation material options available, and their performance both on embodied and operational emissions.
To minimize the embodied carbon of building materials, the industry has mostly focused on major structural materials, such as concrete. This makes sense considering concrete is the world’s highest emitting and most widely used building material. As a result, many strategies and new technologies and strategies are being developed and adopted to reduce concrete-related embodied emissions.
For structural engineers, reducing the embodied carbon of concrete could mean specifying low-emissions concrete mixes or using lighter structures through solutions such as hollow-core concrete slabs. Concrete manufacturers can adopt many low-carbon mix design strategies like switching to Portland-limestone cement (PLC), increasing the percentage of supplementary cementitious materials (SCMs), and allowing longer curing times which means less cement is required. These strategies should be widely adopted and expanded upon. However, the industry should not lose sight of the emission reduction potentials of other building materials.
In Canada, insulation is an essential building material. Insulation materials reduce operational energy and emissions by limiting energy flow through a building’s envelope. But manufacturing insulation can emit significant embodied carbon. As energy codes call for increased efficiency, one of the main solutions is to add more insulation. However, the embodied carbon impact of that additional insulation is often overlooked.
The building industry and policymakers should pay closer attention to the impacts and tradeoffs between both operational and embodied carbon of insulation. Through life cycle assessment (LCA), the “carbon payback” between embodied carbon investment and operational carbon savings can be quantified and optimized.
KPMB Lab recently conducted a study (“KPMB study”) looking at the embodied carbon impacts of extruded polystyrene (XPS), polyiso, spray foam insulation, extruded polystyrene (EPS), stone wool, graphite polystyrene (GPS), fiberglass batt, and blown cellulose insulation. In total, 11 different insulation materials were compared. These results were also used to see how many years it would take for the operational carbon savings to exceed the insulation’s embodied carbon impact.
Embodied carbon of common insulation types
From the KPMB study, the embodied carbon – or Global Warming Potential (GWP) – for the 11 insulation materials is shown in Figure 1. The emissions were calculated per square meter of insulation for a thermal resistance value of 1 (R1) over a 30-year service life. The life cycle stages included in the study were A (material production) to C (end of life). Using this data, KPMB Labs calculated the embodied carbon by varying insulation thicknesses to achieve R1 to R40 (Figure 2). The results showed that:
- XPS insulation was significantly the highest emitting. The embodied carbon of XPS insulation was 15-20 times higher than the other materials. Even the next-generation (lower carbon) XPS products produced after the new 2021 regulation were still twice as high as other insulation types. Note, the KPMB study doesn’t mention if blowing agents were included in the analysis (some LCA tools and EPDs underestimate the emissions from blowing agents).
- Blown cellulose had the lowest embodied carbon. This was due to the minimal processing required to produce it. However, it’s important to keep in mind that the applications for blown cellulose are limited.
- Board or semi-rigid insulations have lower embodied carbon compared to XPS. These included polyiso, EPS, stone wool, and GPS.
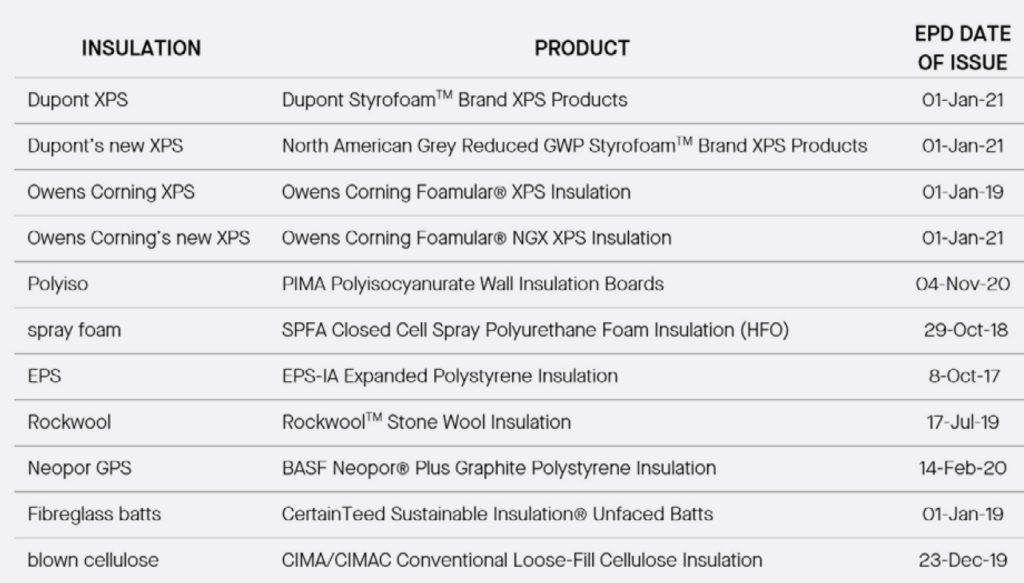
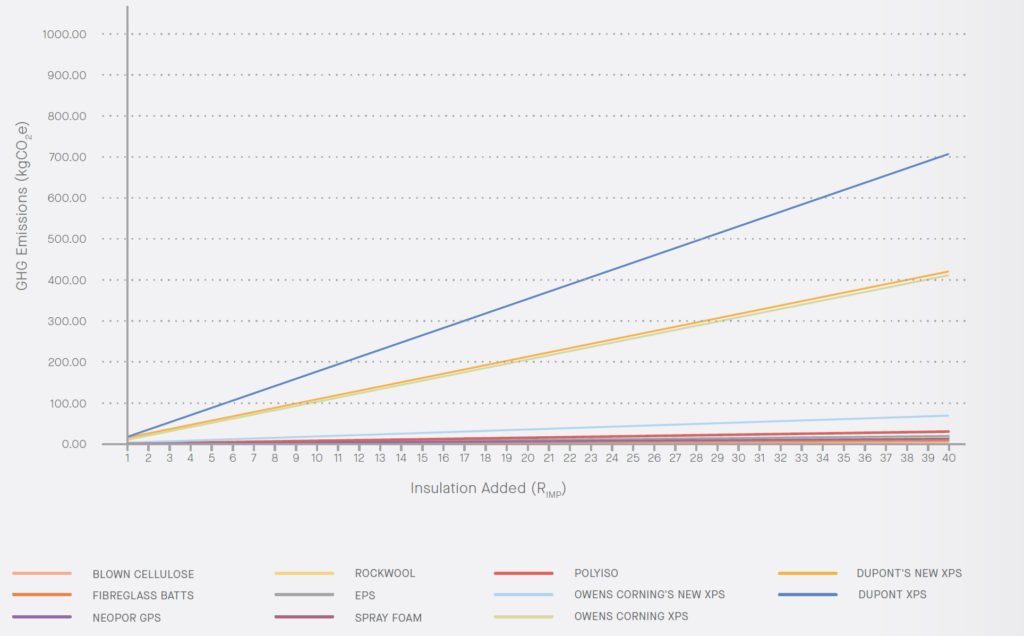
Insulation operational and embodied carbon payback periods
The KPMB study also calculated the carbon payback over 16 years for increasing the effective R-value by increasing the insulation thickness of the 11 types of insulation from R4 to R24. The results for natural gas heated buildings and electric heat pump heated buildings are shown in Figures 3 and 4, respectively. One of the main findings is that there were shorter payback periods for buildings using natural gas heating. This was because the operational emissions were about 12 times higher than the electric heat pump scenario.
In both heating scenarios, the payback period for standard XPS takes significantly longer than all other insulation materials. In fact, the payback period for Owens Corning’s standard XPS and Dupont’s XPS (new or not) wasn’t achievable within 16 years for the electric heat pump scenario. The payback period for blown cellulose, fiberglass batt, GPS, Rockwool, spray foam, EPS, and polyiso was within 1 year for the natural gas heating scenario.
For the natural gas scenario, the new XPS formulation dropped Dupont’s carbon payback from roughly 16 years down to 9 years. Owens Corning’s XPS payback dropped from 9 years to 1.5 years with the new formulation. Even the lowest impact XPS (Ownens Corning’s New XPS) was still significantly longer payback than the other insulation types.

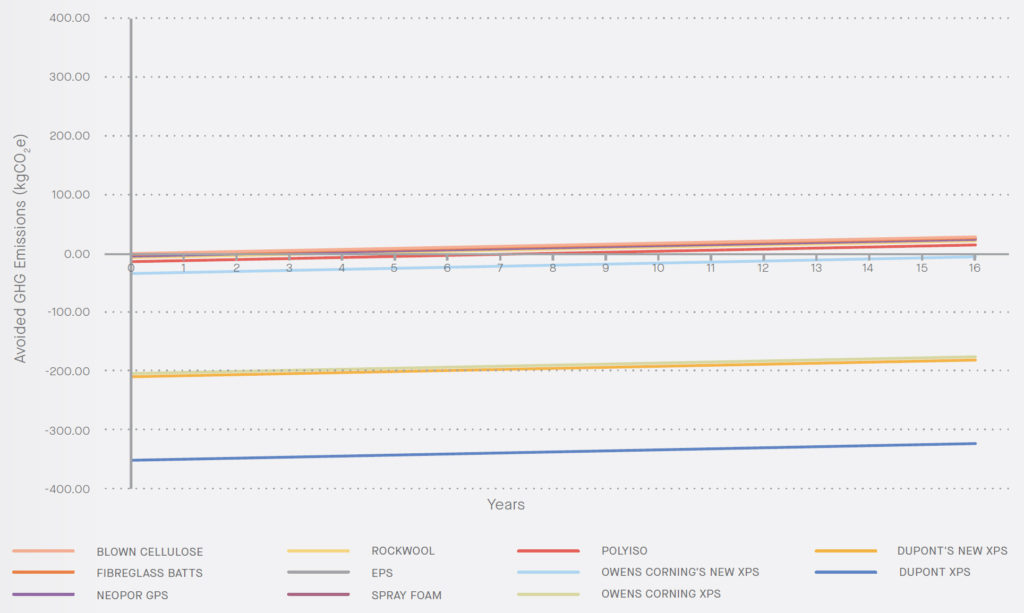
Plant-based insulation
Insulation materials made from “agricultural residues represent a potentially vast sink for atmospheric carbon if a large volume of this biomass was to be gathered and incorporated into buildings” (Chris Magwood, 2019).
Blown cellulose used in the KPMB study is just one type of plant-based insulation available. Hemp, wood, straw, and other cellulose insulations have low embodied carbon compared to more common insulation materials used in Canada (XPS, EPS, and fiberglass batt). Some plant-based insulations are even considered carbon sinks.
Plants (biogenic materials) absorb atmospheric CO2 through photosynthesis and turn it into biomass and also place large quantities of carbon in the soil. If the carbon sequestered out of the atmosphere by plants through this process is greater than the carbon emitted during the extraction, material production, and other life cycle phases, they can be considered carbon sinks. This is the case at least temporarily while the product exists in a building. Because at the end of the product lifetime the biogenic material can decompose, and the carbon stored in plant-based materials can be released back into the atmosphere. This may not happen through alternative end-of-life scenarios.
While using plant-based insulations is yet to become mainstream in Canada, many case studies highlight its benefits and feasibility. Builders for Climate Action compared the upfront embodied carbon of two types of common low-rise buildings in their 2019 white paper. They modeled four building scenarios, which represented high emitting materials, typical, best conventional, and best available material choices, using over 350 materials in their analyses. The results show that buildings can “feasibly reach zero up-front embodied carbon today” by selecting low-carbon building materials, including cellulose and wood fiberboard insulation.
Municipalities are also drawing attention to plant-based insulation to lower embodied carbon in buildings. The City of Nelson, British Columbia recently published its first edition of the Material Carbon Emissions Guide. The guide compiles the results of their Low Carbon Homes Pilot study. The pilot assessed the upfront embodied carbon of 34 Part 9 homes (life cycle stages A1 – A3).
Figures 5 and 6 show the embodied carbon ranges of various insulation types in the Nelson pilot study. The plant-based insulations used are all in the low range and some have negative embodied carbon (are carbon sinks).
However, these numbers shouldn’t be taken as definite. Variations in the sourcing of plant-based materials and associated farming or forestry practices could significantly impact the results. And although some studies only look at cradle-to-grave emissions (A1-A3), what happens at the building’s end of life is also important. If plant-based materials are disposed of rather than re-used, their stored carbon could be released into the atmosphere. Even the disposal details matter, for example, how much decomposition occurs and if landfill methane is captured.
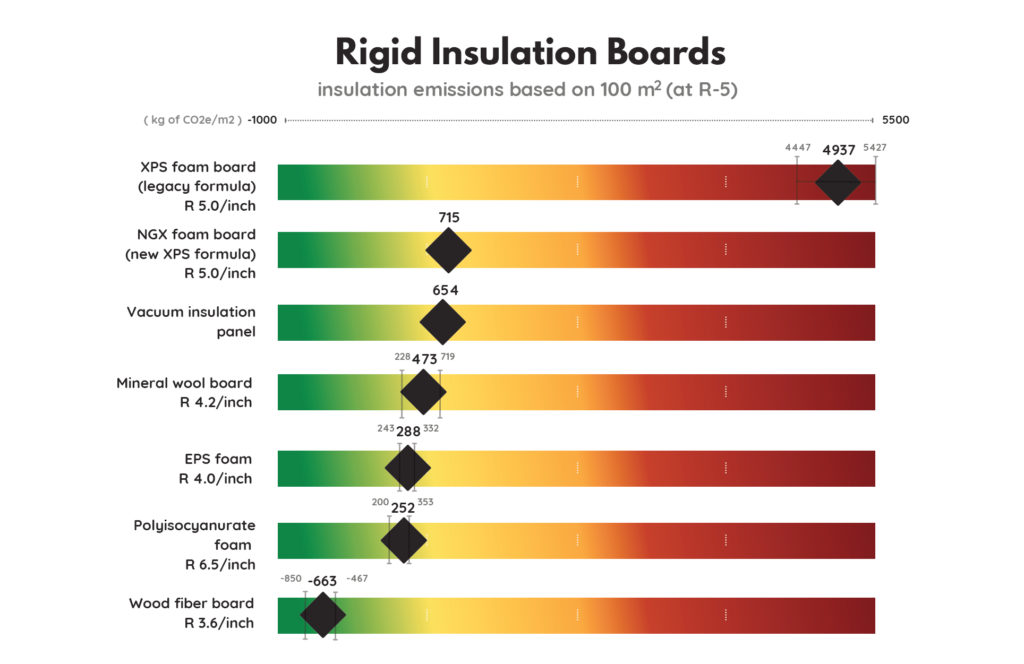
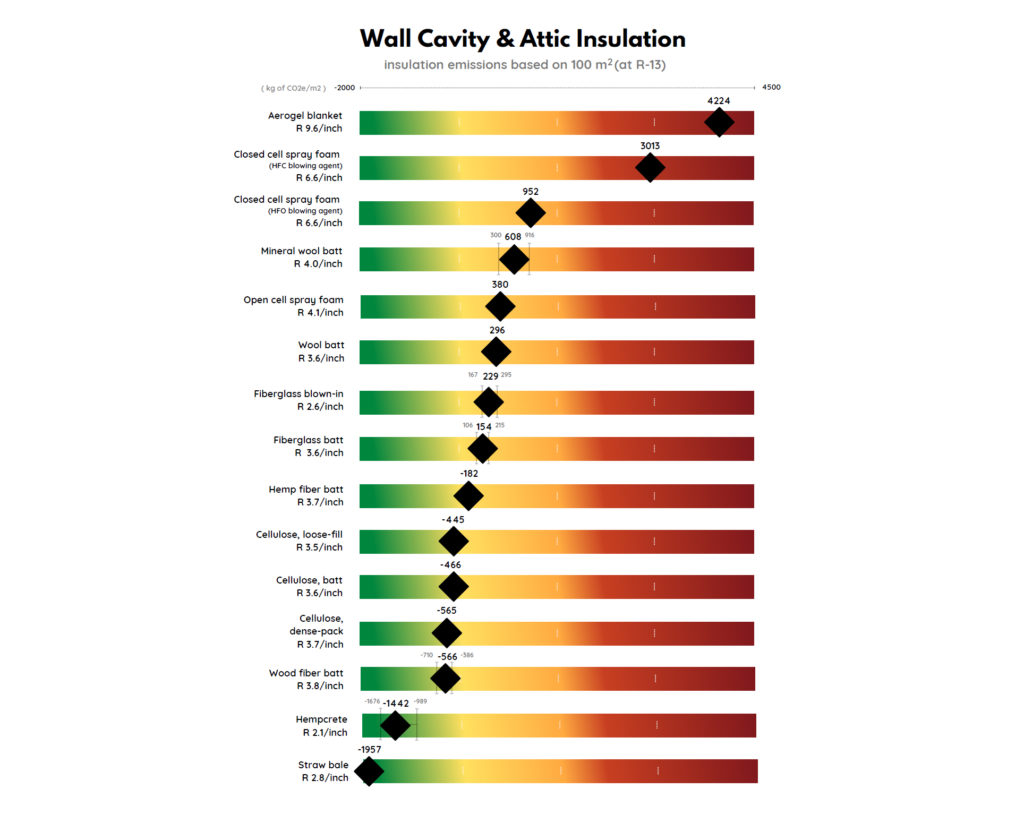
Conclusion
The embodied carbon results in the KPMB study showed that XPS insulation is a clear outlier among common insulation materials. XPS insulation had up to 15-20 times higher emissions than the other insulation materials. Only the lowest impact new XPS formulation by one manufacturer came close to other insulation types, however, still had a longer carbon payback than other types of insulation. For similar applications, alternatives to XPS with lower embodied carbon are available on the market, like mineral wool. Blown cellulose had the lowest embodied carbon among all insulation materials analyzed. Project teams should explore the feasibility of using plant-based insulation, like blown cellulose – not only reduce embodied carbon but for its carbon-storing capacities.
Mantle Developments can help you select the best low-carbon materials for your project.
Contact us to measure your project’s emissions and reduce the embodied carbon of your construction materials. We can provide LCA and embodied carbon assessments, help you find readily available low-carbon materials, connect you with local suppliers, and help develop strategies supporting low-carbon and net-zero developments.