Though mass timber offers many benefits over traditional building materials, its renewable nature and negative carbon impact are perhaps the most exciting. Turning trees into timber emits fewer greenhouse gases than the manufacture of traditional building materials like steel and concrete. That alone is a carbon benefit. However, it’s the carbon that is removed from the atmosphere and stored in the wood — the sequestered carbon — that is the real game-changer. It means that mass timber has the potential to be more than just a carbon-light construction method. It can become a carbon sink. Industry advocates claim that by 2034, the North American construction industry as a whole will store more carbon than it emits.
Fig. 1, Mass Timber Report 2020 pg. 5
Operational and Embodied Carbon Emissions
Dramatically reducing the carbon emissions from the construction industry is a priority in order to reach emission reduction targets. Currently, construction materials are responsible for around 11% of global greenhouse gas (GHG) emissions. Given the scale of new construction planned globally and the lack of market-ready at-scale decarbonization strategies for construction material production, this number could increase relative to many other major contributors like industry (30%), transportation (22%), and building operations (28%). To understand why, we have to understand the difference between the impact of operational carbon and embodied carbon.
At Mantle314 we shine a light on climate risks and opportunities for business, and advance strategies to thrive. We see embodied carbon as one of the most important climate opportunities over the next decade since it is not widely well understood or managed, and has huge potential risks. We help government and business leaders make decisions to reduce their embodied carbon footprint. To learn more, read our research on the topic in reports such as this TD Future Cities Centre – Net Zero Carbon Construction Report.
Operational carbon is emitted from the annual running of a building: typically from the electricity and natural gas required to heat, cool, ventilate, light and power plug loads of the building. Embodied carbon is emitted during the manufacture and transport of the materials used to construct the building.
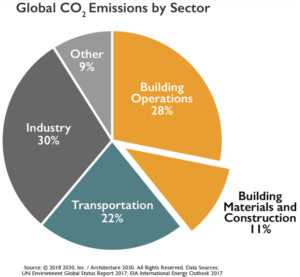
For most projects, operational carbon is emitted each year and by the end of the building’s life cycle it is larger than embodied carbon. However, each year’s impact is small relative to the embodied carbon, which is mostly emitted during construction. This means that for the first several years of a building’s life, embodied carbon is the dominant source of carbon.
This leads to three reasons why over the next decade or so, embodied carbon in the built environment is a particularly important issue. Firstly, for new construction projects built today as shown below in the graph Total Carbon Emissions of Global New Construction from 2020-2050, by 2030 74% of carbon emissions will come from their embodied carbon, and only 26% from their operational carbon. This means that to meet short-term carbon emission goals (under the Paris Agreement, Canada is committed to reducing emissions by 30% below 2005 levels by 2030), reducing embodied carbon must be a priority.
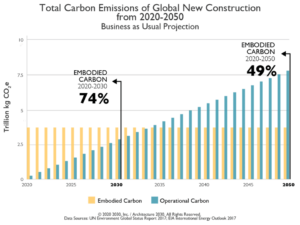
Secondly, as electric grids increase their share of renewable energies and decarbonize, operational carbon of new construction is decreasing more quickly than embodied carbon.
Thirdly, new construction has increasingly strict limits placed on operational carbon. Building codes require a minimum level of energy efficiency, which means new construction emits less operational carbon than previously, and with each code update the efficiency requirements increase. There are currently no such regulatory requirements on embodied carbon in most places. The materials we build from can be extremely polluting and can be shipped from across the world. Why are we heavily regulating operational carbon but ignoring embodied carbon? Embodied carbon regulations are starting to be introduced in progressive jurisdictions. Many of them are looking at mass timber as a win-win-win.
Avoiding and Sequestering Carbon
So how does mass timber reduce the embodied carbon of buildings? And how likely is it that the industry will achieve net negative emissions?
There are two reasons for mass timber’s beneficial embodied carbon impact. The first is the avoided emissions when compared to traditional building materials like concrete and steel. The second is the sequestered carbon pulled from the atmosphere and stored in the wood
Avoided emissions are rather straightforward. The manufacture and transport of mass timber uses less energy and emits less carbon than similar processes for concrete or steel (Figure 4 below). For an amount of product with the same amount of strength, mass timber emits fewer GHGs.
Fig. 4, CO2 emissions from equivalent designs of a large office building
Sequestering carbon is slightly more complicated. When trees grow, they take CO2 from the atmosphere and turn it into wood through photosynthesis, where sunlight and chlorophyll convert CO2 and water into wood, until through decomposition it returns to the atmosphere.
Some argue that sequestration shouldn’t be included in any embodied carbon calculation. If after the building’s useful life cycle the timber ends up rotting, the sequestered carbon in the wood will be returned to the atmosphere. This might be true if the mass timber is left to rot in an unmanaged landfill, but that is not a likely outcome. There could be many potential uses for mass timber decommissioned from a building including reuse in furniture and other non-structural decorative applications like internal finishings. Any landfill that accepts timber would likely employ methane capture and reuse meaning only a fraction of the carbon would be released to the atmosphere.
There is a net reduction in atmospheric carbon even in the unlikely event that all trees or mass timber elements eventually rot and their carbon returns to the atmosphere as long as the wood is harvested from responsibly managed forests without clear cutting. This is because a portion of the carbon removed from the atmosphere during tree growth gets stored in the soil. So even if carbon sequestered in wood returns to the atmosphere, the responsibly managed forest as a whole remains a carbon sink.
Mass timber carbon life-cycle
Sequestration at the forest level requires sustainable timber harvesting. As we briefly discussed in a recent blog post, the most basic measure of sustainable forestry is sustained yield – that the harvest rate is at or below the forest’s new growth rate (this makes clear why sequestration is only relevant for sustainably managed forests; if the whole forest was clear cut after 50 years, there would be no new growth and no further sequestration). Furthermore, much of the carbon fixed into the soil would be emitted to the atmosphere.
However, some certifications have detractors. Some accuse the certifications of allowing certain forestry companies to “greenwash” their practices, flaunting sustainable practices or even using illegally harvesting approaches, without losing their FSC label. They have also been criticised for their position on plantations – monoculture forests that exist to be harvested – which ecologists say create a biodiversity “desert”. For a deeper dive into the complexities of sustainable forest management, listen to this podcast episode where 21st Century Imperative’s Craig Applegath interviews Dale Prest, CEO of the Climate Forest Company extensively about the topic. Craig is principal and architect at DIALOG and chairperson of the Mass Timber Institute,
On another episode of the podcast, Mantle314’s Co-founder and Chief Operating Officer, Ryan Zizzo, spoke with Craig about another critical issue in mass timber sustainability: verification. It can be hard to independently verify the provenance of wood that arrives at a factory or construction site: it may be labeled as FSC certified, but similar to bankers’ packing of subprime loans into prime securities, if sawmills slip some unsustainably harvested timber into an otherwise certified batch, it can be near impossible for the final customer to confirm that the timber was indeed sustainably harvested.
These challenges present a potential roadblock to the otherwise sunny picture of mass timber’s transformative environmental potential. Not only do any discussions of the mass timber industry growth need to be accompanied by an examination of sustainable forestry practices, the industry as a whole needs to research and implement more reliable ways to ensure that sustainable practices can be verified transparently down the supply chain. This issue is solvable in theory: blockchain technology with DNA markers could be used to link individual pieces of wood to specific forests, an area where additional research and development is required.
Despite these challenges, the carbon benefits possible from well-managed mass timber make the extra effort worth it. Mass timber is currently the most carbon-efficient building material for multi-storey construction. Even without considering carbon sequestration, prioritizing more mass timber would result in a significant drop in avoided carbon emissions.
Indigenous Partners
We believe Indigenous communities in Canada make particularly strong partners in forestry for mass timber. Indigenous communities are the original stewards of Canada’s forests, and have ancient histories of sustainable forest management. Sawmills and mass timber production facilities can bring needed employment and economic development to these remote communities. Mass timber investments should prioritize working together with Indigenous communities to sustainably utilize their forestry resources towards mass timber for benefits to both the climate and the economy.
For all of these carbon benefits, the growth of mass timber construction is one of the key strategies to decarbonize the building sector. We encourage everyone in the construction sector to familiarize themselves with mass timber and consider if it’s a fit for your future projects.
Thank you to Suhayl Chettih, MBA Candidate, Harvard Business School, for his contribution to this research and article.
Contact us to help manage your climate risk
Mantle works with real estate owners/developers, built environment designers, and policymakers interested in climate-smart construction including the use of mass timber and other low carbon construction materials. We implement green building best practices including Zero Carbon Building standards, LEED, and embodied carbon analysis and reduction strategies.
Contact us today to give your organization a competitive advantage on climate change.