When we talk about a bold new green technology that could radically transform our society, the mind goes first to renewable energies, biodegradable plastics, electric vehicles. But one of today’s most exciting green technologies is also one of humanity’s oldest: wood.
Timber used to be humankind’s primary building material, until concrete and steel took center stage near the end of the 19th century. With the technological breakthrough of steel-reinforced concrete, these materials offered protection from fire and structural strength at economics that allowed us to build skyscrapers, enabling the urbanization that defined the 20th century. They solved the problems of construction in the 20th century: how to build more, build higher, build cheaply, and build safely.
But now already well into the 21st century, our built environment has brought us new problems which need new solutions. How can we keep climate change from destroying our way of life? How can we equitably maintain a modern standard of living without depleting the earth’s natural resources? How do we build the millions of new housing and commercial units our growing world demands without warming the earth beyond acceptable limits? How to change “green living” from a luxury good to an affordable, even necessary part of our built environment?
Mass timber is one of our best answers to these fundamental 21st century challenges, and Canada is a natural fit to take a leading role in this exciting new industry. However, mass timber is not here to fully replace concrete and steel: there will always be a need for these traditional materials which have a wide array of important applications. We believe mass timber should be added to this mix to become another primary material considered for any building. We at Mantle314 have been working for years to bring our climate expertise into business decisions, and so we speak with confidence when we say that mass timber shows great promise, both for business and for climate.
Of its many advantages, we highlight the following 4 as the primary drivers of mass timber’s growing success:
- Sustainable: mass timber is a carbon sequestering material that substitutes for concrete and steel, which emit an estimated 11% of global GHG emissions (UN Global Environment Status Report 2017, EIA).
- Safe: mass timber is fire resistant, burning slowly and predictably, versus steel which melts under high temperatures; mass timber performs well in seismic events.
- Strong: mass timber is strong enough to build 35+ storey buildings (the size of Sidewalk Toronto’s planned mass timber development); newest North American building codes will allow for 12 or 18 storey buildings.
- Cost-effective: mass timber allows for quicker construction with less crew, and can theoretically be cheaper to build than concrete or steel in the 4 to 18 story range.
If you are interested in learning more about mass timber’s engineering properties and safety performance, such as its structural integrity, fire performance, seismic performance, and so on, we recommend reading Chapter 5 of 2020’s Mass Timber Report).
Mass timber industry groups such as Think Wood and Wood Works point out several other advantages of mass timber. Exposed wood is desirable by occupants and can lead to higher tenant satisfaction and higher rents. Modular construction techniques can greatly reduce the cost and time needed for construction, and allow for rapid scale. There is research suggesting that wood has a “biophilic” effect on people, where being in wooden buildings can improve residents’ health and well-being. By allowing for quicker construction times with less labour, mass timber has the potential to increase construction sector productivity, a sector notorious for stagnant productivity growth.
That’s not to say that mass timber does not have its issues. To build in mass timber in North America today means many extra steps and challenges, preventing more widespread usage of this new material. Some of the key factors challenging the sector are:
- Supply chain gaps: North American mass timber production has increased >1000% since 2010, however, many major metro areas have very little – if any – local mass timber production. Several high profile mass timber projects have used mass timber imported from Austria.
- Distribution challenges: mass timber is costly and complex to ship over long distances, especially by land. At current rates, it can be cheaper to import mass timber from Europe by sea than to transport it from BC to Ontario over land.
- Building code compliance: mass timber buildings will finally be included in the 2020 NBCC (Canada) and 2021 IBC (US) for up to 12- and 18-story buildings respectively. However, in these codes mass timber must be 100% encapsulated, meaning any developer wanting the benefits of exposed mass timber will still need additional approvals.
- Cost: mass timber can theoretically be cheaper to construct, however however according to mass timber construction specialist Mark Gaglione at Ellis Don, in the Toronto market mass timber buildings higher than 6 storeys carry a ~10% price premium compared to traditional cast-in-place concrete (shorter buildings are often built with light-wood frames which are even cheaper). Whether further development of the industry will enable this price to come down or not is disputed.
There are further difficulties as well that we will explore in our later blog posts, such as ensuring that mass timber is sustainably harvested (without which it loses its carbon benefit), achieving the faster build time promised by mass timber, and with the lack of skilled tradespeople in the industry.
But… What Actually is Mass Timber?
You may have heard first about mass timber through its highest profile family member: cross-laminated timber, or CLT. CLT is a key member of the mass timber family of products, a family which makes up the mass timber building system, engineered wood products that enable large-scale construction that would not be possible with raw lumber or light-wood framing. They are engineered because they take cuts of dimension lumber (often softwoods like spruce, pine, and fir) and are pressed and glued together – laminated. This process results in products that are significantly stronger than their non-engineered timber parts.
Different products in the mass timber family are configured and laminated differently. One way to understand the different products is to divide them into panels and beams. Panels are large slabs used for walls, floors, and roofs; a typical panel is 1-3 meters wide and can be up to 18 meters long. Beams are long and sturdy, used for horizontal or vertical weight bearing applications and can be anywhere from 3 to 20 meters long. The classic mass timber configuration is CLT panels with Glulam beams.

Mass Timber Product Family
CLT panels are made by stacking, pressing, and laminating dimension lumber in perpendicular layers. Panels are usually 3, 5, or 7 layers thick – the panel’s “ply”. The perpendicular layering gives panels 2-dimensional strength, which allows for greater flexibility in building applications. UBC’s Brock Commons dormitory building for example was able to forgo horizontal beams, since the 2-dimensional strength of the CLT panels let them be placed directly on vertical glulam columns.
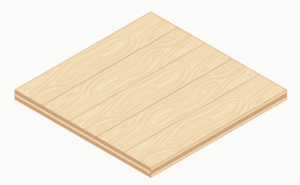
Glulam beams are made by stacking, pressing, and laminating dimension lumber in a single direction. Glulam production is actually a method for creating strong beams that dates back over 100 years and is recently going through a resurgence as part of the mass timber building system. Glulam has strong one-dimensional strength and is suitable for horizontal and vertical load bearing applications.
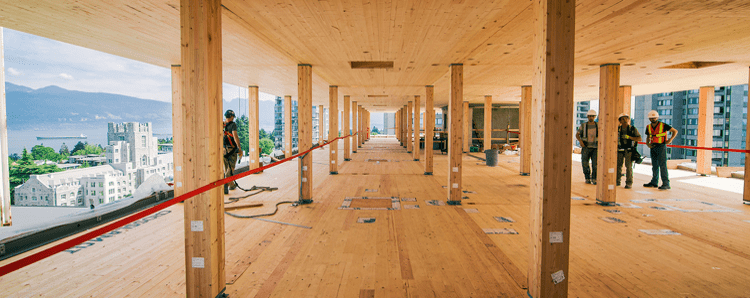
Glulam as vertical columns in UBC’s Brock Commons
There are several other products in the mass timber family. Similar to CLT, variants like DLT (dowel-laminated timber), NLT (nail-laminated timber), and GLT (glue-laminated timber; GLT is just glulam in panel form) serve a similar structural purpose. There are also several Structural Composite Lumbers (SCL), other engineered wood products that have been in use in lightwood framing for decades, such as LVL (layered veneer lumber), PSL (parallel strand lumber), and OSL (oriented strand lumber) which are sometimes used as part of the mass timber building system (for more details about all of the products in the mass timber family, check out Chapter 1 of the 2020 Mass Timber Report).
Mass timber is also commonly used in hybrid with traditional building materials, for reasons ranging from cost, to structural stability, aesthetics, or building code requirements. Many mass timber buildings will have a concrete foundation, use a concrete core for stability or fire access, or be built with steel elements. Other configurations using alternative timber products are also quite common: mass timber flooring used in a building with steel and concrete vertical load bearing, or like Minneanopolis’ T3 building which used NLT panels over glulam beams.
Selection of Mass Timber Projects
There have already been several mass timber buildings built in North America that showcase its versatile applicability as a building material, such as the Brock Commons Tallwood House, a student residence at the University of British Columbia and at its completion the world’s tallest mass timber tower (a prize taken by Norway’s Mjøstårnet in 2019).
Brock Commons Tallwood House UBC
Architect: Acton Ostry Architects Inc.
Location: UBC Campus, Vancouver, BC, Canada
Function: Student Residence
Date completed: July 2017
Size: 18-story, 15,000 m2
Brock Commons was built as a student residence on the UBC campus in Vancouver as a proof of concept for sustainability, speed, and cost in tall mass timber construction. The building was built using a digital-first building information modeling design process, which allowed for all the building materials to be completely prefabricated and then assembled onsite. This resulted in an estimated 4 months quicker construction time. FPInnovations estimated that the building avoided emitting an equivalent of 2,400 tons CO2 compared to an equivalent structure.
Brock Commons is a hybrid mass timber building, with a concrete foundation, 1st story podium, and full-height concrete cores housing elevator and utility shafts, enclosed in a mass timber superstructure of CLT panels on glulam columns.
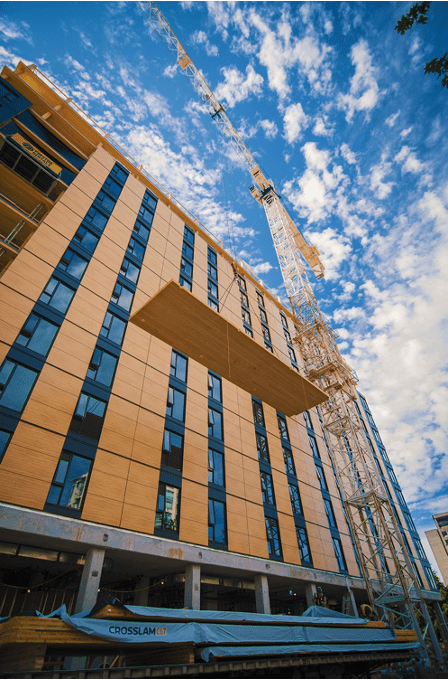
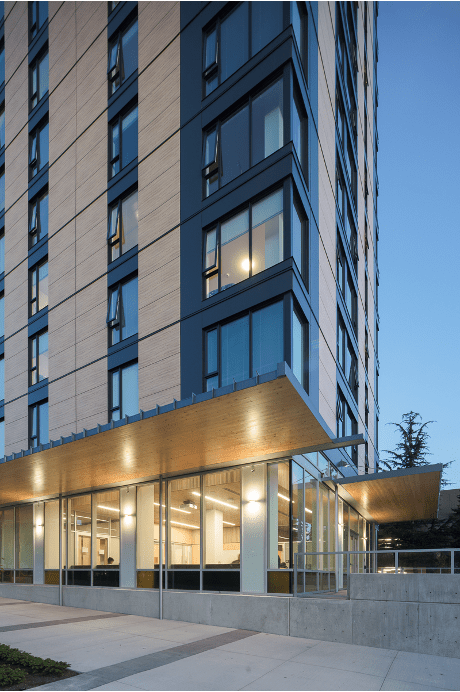
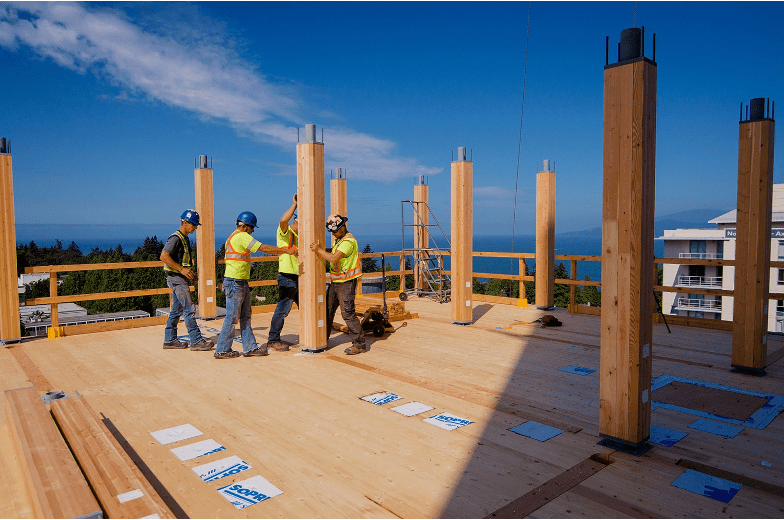
Source: Seagate Mass Timber
T3 Bayside
Architect: 3XN
Location: Bayside District, Toronto, Ontario, Canada
Function: Office
Date completed: planned 2023
Size: 10-story, 23,000 m2
T3 Bayside is planned to be the tallest timber office building in North America, the first office building in Toronto’s Bayside District development. The building will use exposed CLT panels, with the developer Hines claiming it as a differentiator for quicker leasing and higher rents (as they did for their similarly named T3 Minneapolis office tower, completed in Nov 2016).
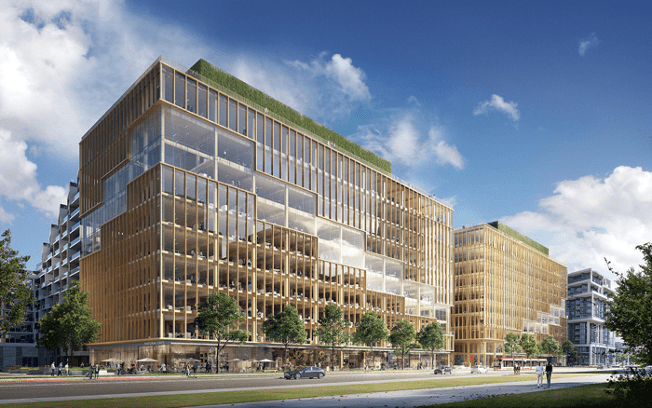
Source: T3 Bayside
UMass Amherst Design Building
Architect: Leers Weinzapfel Associates
Location: UMass Amherst Campus, Amherst, MA, USA
Function: Educational
Date completed: Jan 2017
Size: 4-story, 8,000 m2
UMass Amherst’s Design Building houses its programs of Landscape Architecture, Architecture, and Building Technology, built in mass timber to demonstrate the school’s commitment to sustainable design. The Design Building was the largest academic mass timber building in the US (until University of Arkansas’ Adohi Hall opened in Nov 2019). An estimated 2,600 tonnes CO2 was avoided by using mass timber rather than traditional building materials.
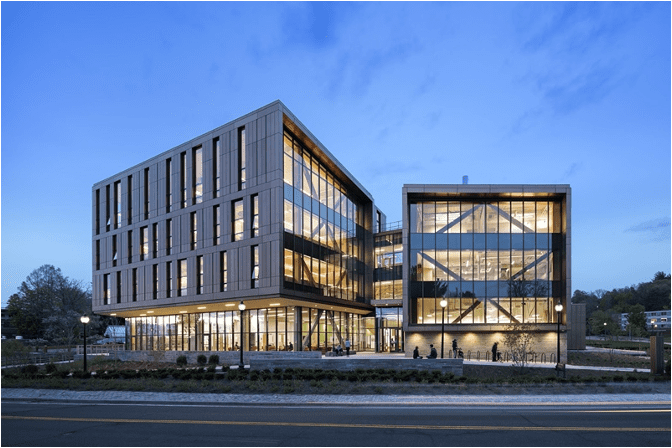
Source: Think Wood
Canada Should Be the Global Leader in Mass Timber
Here at Mantle314, we believe that Canada is a natural fit to become the world leader across the mass timber value chain, from sustainable forestry and mass timber production to architecture, design, and research. Towards this end, Mantle314 has joined the Mass Timber Institute at the University of Toronto and a consortium of mass timber industry suppliers led by Ontario’s sole local mass timber producer, Element5. Through these partnerships and more we believe that Canada can lead this exciting new green industry.
Canada has abundant natural forestry resources – in fact, Canadian forests have been under-harvested for decades. Sustainable forestry practices require sustained yield: a certain level of allowable harvesting equal to a forest’s natural rate of growth, that ensures healthy growth and no loss of forest land. Canada has harvested below this amount for decades (~70% in 2015), meaning that Canada has still great potential in sustainably harvesting timber.
Sustainable forestry also aligns with Canadian goals to promote the economic development of indigenous communities. As the original practitioners of sustainable forestry management (ages before the term would even be used to refer to the practice), Canada’s First Nations are stewards of Canada’s bountiful forestry resource. Involving these communities as key partners in forestry initiatives and prioritizing them as suppliers for timber resources used in mass timber production can be one way to support their sustainable economic development. We can already see success cases such as the White River Forest Products Ltd company, which is the primary supplier for Element5’s St. Thomas, Ontario mass timber factory. White River Forest Products is a community-based joint venture partially owned by the Netamisakomik Anishinabek (Pic Mobert First Nation).
Canada already is a global leader in transformative green industries, from strict emission reduction targets to renewable energy production. Canada has the opportunity to set a global example in sustainable building, and export that industry abroad. Though currently the European mass timber industry is significantly more advanced than in Canada or the US, no European company has a strong foothold in North America, where the mass timber market is expected to grow exponentially. Canadian producers have already started to build factories in the US (such as Structurlam’s newest Conway, Arkansas plant, which will supply the mass timber being used to construct Walmart’s new HQ). With the right public policy that supports research, coordination, and investment in mass timber, Canada can develop local expertise in mass timber and become a global leader in this new transformative industry.
Thank you to Suhayl Chettih, MBA Candidate, Harvard Business School, for his contribution to this research and article.
Contact us to help manage your climate risk
Mantle314 works with real estate owners/developers, built environment designers, and policy makers interested in climate smart construction including the use of mass timber and other low carbon construction materials. We implement green building best practices including Zero Carbon Building standards, LEED, and embodied carbon analysis and reduction strategies.
Contact us today to give your organization a competitive advantage on climate change.